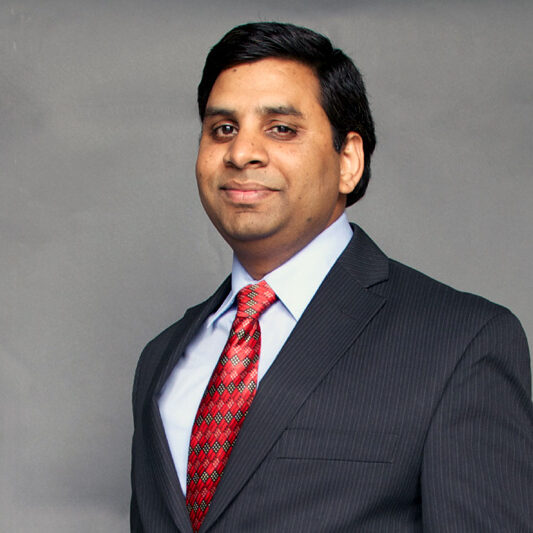
Chandra Veer Singh | BSc (Dayalbagh), MTech (IISc), PhD (Texas A&M), PEng
Professor
Office: WB 137
T: 416.946.5211
E: chandraveer.singh@utoronto.ca
Research Group: Laboratory for Computation Materials Engineering
Research Areas
Computational materials science:
Density functional theory (DFT), molecular dynamics (MD), Multiscale modeling.
2D materials:
Graphene, graphene oxide, Borophene, MoS2, TMDs, MXenes.
Machine learning:
For processing-structure-property relationships, alloy design, catalyst design, and development of interatomic potentials and force fields.
Energy conversion and storage:
Metal-ion batteries, CO2 reduction, Photocatalysis; Hydrogen production and storage.
Failure of advanced materials:
Understanding damage and failure at multiple length and time -scales in metals, alloys and composites.
Research Clusters
Dr. Singh is the Erwin Edward Hart Endowed Associate Professor of Materials Science and Engineering, and the Associate Chair of Research for the MSE department, with an expertise in computational materials engineering. His research group focuses on atomistic and multiscale modeling of materials, using techniques such as density functional theory, molecular dynamics and machine learning. His group has contributed significantly to the design and development of graphene and other 2D materials for energy storage and structural applications. He has authored more than 100 peer-reviewed publications; including in esteemed journals such as Advanced Materials, Science Advances, Nature Catalysis, PNAS, Nature Communications, Energy & Environmental Science, JACS, Energy Stoage Materials, and Nano Letters. He has also won several prestigious awards such as Ontario New Researcher Award, $1M Connaught Global Challenge (team award), Hart Professorship, and NSERC Accelerator Supplement. During last seven years at UofT, he has trained over 80 graduate students and postdoctoral researchers. He is a member of Compute Canada Resource Allocation Committee and TMS ICME committee, and actively participates in journal paper and grant reviewing at the international level.
Professional Memberships
- Professional Engineers Ontario (PEO)
- Materials Research Society (MRS)
- The Minerals, Metals & Materials Society (TMS), Lifetime Member
- American Chemical Society (ACS)
- The American Society of Mechanical Engineers (ASME)
Link to Google Scholar
Select Publications:
- Chen, L., Chen, Z. W., & Singh, C. V. (2020), “Insights on the Dual Role of Two-Dimensional Materials as Catalysts and Supports for Energy and Environmental Catalysis”, Journal of Materials Chemistry A, published online. DOI: 10.1039/D0TA08649E
- M Akhshik, M, Panthapulakkal, S., Tjong, J., Bilton, A., Singh, C.V., Sain, M., (2020), “Cross-country analysis of life cycle assessment–based greenhouse gas emissions for automotive parts: Evaluation of coefficient of country”, Renewable and Sustainable Energy Reviews, 110546. DOI: 10.1016/j.rser.2020.110546
- Lu, Z., Chen, Z. W., & Singh, C. V. (2020), “Neural Network-Assisted Development of High-Entropy Alloy Catalysts: Decoupling Ligand and Coordination Effects”, Matter, published online. DOI: 10.1016/j.matt.2020.07.029
- D Chen, Z Chen, Z Lu, X Zhang, J Tang, CV Singh (2020), “Transition metal–N 4 embedded black phosphorus carbide as a high-performance bifunctional electrocatalyst for ORR/OER”, Nanoscale, 12 (36), 18721-18732. DOI: 10.1039/D0NR03339A.
- W.S. Huxter, C.V. Singh, and J. Nogami (2020), “Hindered surface diffusion of bonded molecular clusters mediated by surface defects”, Physical Review Materials, 4, 093401.
- Dhaliwal, P.B. Nair, and C.V. Singh (2019), “Uncertainty analysis and estimation of robust AIREBO parameters for graphene”, Carbon, 142, 300-310.
- F. Najafi, G. Wang, S. Mukherjee, T. Cui, T. Filleter, and C. V. Singh (2020), “Toughening of graphenebased polymer nanocomposites via tuning chemical functionalization”, Composites Science and Technology, 194, 108140. DOI: 10.1016/j.compscitech.2020.108140
- D Chen, Z Chen, X Zhang, Z Lu, S Xiao, B Xiao, and C.V. Singh (2020), “Exploring single atom catalysts of transition-metal doped phosphorus carbide monolayer for HER: A first-principles study”, Journal of Energy Chemistry, 161, 570-576. DOI: 10.1016/j.jechem.2020.03.061
- M. A. Daly, A. Kumar, C. V. Singh, and G. D. Hibbard, “On the competition between nucleation and thickening in deformation twinning of face-centered cubic metals”, International Journal of Plasticity, 130, 102702. DOI: 10.1016/j.ijplas.2020.102702
- M Jiang, H Gong, H Xiao, CV Singh, Z Liu, L Qiao, X Zu (2020), “Effects of temperature and energy on the radiation response of GaAs/AlAs and GaAs/AlGaAs superlattices”, Radiation Physics and Chemistry, 108983. DOI: 10.1016/j.radphyschem.2020.108983
- S. Mukherjee, L. Kavalsky, and C.V. Singh (2020), “Dramatic improvement in the performance of graphene as Li/Na battery anodes with suitable electrolytic solvents”, Carbon, 161, 570-576. DOI: 10.1016/j.carbon.2020.02.001
- Peng, H. Sun, A.P. Gerlich, W. Guo, Y. Zhu, L. Liu, G. Zou, C.V. Singh, Y. N. Zhou (2019), “Near-ideal compressive strength of nanoporous silver composed of nanowires”, Acta Materiala, 173, 163-173.
- Qian, W. Sun, D.L.H. Hung, C. Qiu, M. Makaremi, S.G.H. Kumar, L. Wan, M. Ghoussoub, T. Wood, X. Xia, A. Tountas, Y.F. Li, L. Wang, Y. Dong, I. Gourevich, C.V. Singh, and G.A. Ozin (2019), “Catalytic CO2 reduction by palladium decorated silicon hydride nanosheets”, Nature Catalysis, 2, 46-54.
- Sun, Z. Shi, S. Mukherjee, and C.V. Singh (2019), “Elastomer-like deformation in high-Poisson's-ratio graphene allotropes may allow tensile strengths beyond theoretical cohesive strength limits”, Carbon, 143, 752-761.
- Kavalsky, S. Mukherjee, and C.V. Singh (2019), “Phosphorene as a catalyst for highly efficient nonaqueous Li-air batteries”, ACS Applied Materials & Interfaces, 11:1, 499-510.
- Mukherjee, L. Kavalsky, and C.V. Singh (2018), "Ultrahigh storage and fast diffusion of Na and K in blue phosphorene anodes", ACS Applied Materials & Interfaces, 10 (10), 8630–8639.
- Cao, S. Mukherjee, J. Y. Howe, D.D. Perovic, X. A. Sun, C.V. Singh, Y. Sun, T. Filleter (2018), “Nonlinear fracture toughness measurement and crack propagation resistance of functionalized graphene multilayers”, Science Advances, 4(4), eaao7202.
- O'Brien, P., Ghuman, K., Jelle, A., Sandhel, A., Wood, T., Loh, J., Jia, J., Perovic, D., Singh, C. V., Kherani, N., Mims, C., Ozin, G., (2018), “Enhanced photothermal reduction of gaseous CO2 over silicon photonic crystal supported ruthenium at ambient temperature”, Energy and Environmental Science, 11, 3443-3451.
- Grixti, S. Mukherjee, and C.V. Singh (2018), “Two-dimensional boron as an impressive lithium-sulphur battery cathode material”, Energy Storage Materials, 13, 80-87.
- Li, Chen, L., Mukherjee, S., Gao, J., H. Sun, Liu, Z., Ma, X., C. V. Singh, Ren, W., Cheng, H.M., and N. Koratkar (2017), “Phosphorene as a polysulfide immobilizer and catalyst in high-performance lithium-sulfur batteries”, Advanced Materials, 29(2), 1602734.
- M.A. Daly, C. Cao, H. Sun, Y. Sun, T. Filleter, and C. V. Singh (2016), “Interfacial Shear Strength of Multilayer Graphene Oxide Films”, ACS Nano, 10 (2), 1939–1947.
- Ghoussoub, S. Yadav, K. K. Ghuman, G. A. Ozin, and C. V. Singh (2016), “Metadynamics-biased ab initio molecular dynamics study of heterogeneous CO2 reduction via surface frustrated Lewis pairs”, ACS Catalysis, 6, 7109–7117.
- K. Ghuman, L. Hoch, P. Szymanski, M. El-Sayed, J. Loh, N. Kherani, G. A. Ozin, and C. V. Singh (2016), “Photo-excited surface frustrated Lewis pairs for heterogeneous photocatalytic CO2 reduction”, Journal of the American Chemical Society (JACS), 138, 1206–1214.
- Montesano, H. Chu, and C. V. Singh (2016), “Development of a physics-based multi-scale progressive damage model for assessing the durability of wind turbine blades”, Composite Structures, 141, 50–62.
- Yadav, Z. Zhu, and C. V. Singh (2014), “Defect engineering of graphene for effective hydrogen storage”, International Journal of Hydrogen Energy, 39, 4981-4995.
Book
Talreja R and Singh CV. (2012) Damage and Failure of Composite Materials, Cambridge University Press, London. ISBN: 9780521819428, DOI: 10.1017/cbo9781139016063
MSE438: Computational Materials Design
MSE351: Design and Simulation of Materials Processes
- NSERC Discovery Accelerator Supplement, 2018
- Erwin Edward Hart Professorship in Materials Science and Engineering, 2016
- Ontario Early Researcher Award, 2016
- Connaught Global Challenge Award (team award), 2015
- Connaught New Researcher Award, 2015