On September 23rd, over 30 undergraduate, graduate students, along with postdoctoral fellows from the Department of Materials Science and Engineering (MSE) participated in an industrial tour coordinated by Laboratory for Extreme Mechanics & Additive Manufacturing (LEMAM, Prof. Zou’s Research Group) and MSE Graduate Student Association (MSEGSA), The tour was sponsored by the Ontario Vehicle Innovation Network’s Regional Future Workforce (RFW) Program.
The day trip included visits to three leading manufacturing companies in Ontario: Burloak Technologies, Exco Engineering, and Magna International. While each company employed various manufacturing techniques, a common theme was the integration of additive manufacturing technologies to enhance Canadian manufacturing. This tour provided MSE students with valuable insights into industry operations, networking opportunities, and potential career paths.
Additive Manufacturing at Burloak Technologies
The first stop was Burloak Technologies, a leader in additive manufacturing, specializing in 3D printing solutions that are transforming traditional manufacturing processes. Students were given a detailed tour of the various stages of additive manufacturing, from design and prototyping to post-processing and final product development. They observed firsthand how complex geometries, often difficult or impossible to achieve using conventional methods, are efficiently produced through advanced 3D printing technologies. The tour also included an engaging discussion on the future of additive manufacturing, providing students with valuable insights into the industry’s evolving landscape.
At Burloak Technologies, students explored cutting-edge additive manufacturing systems, including laser powder bed fusion (LPBF) and electron beam melting (EBM). The post-processing techniques, such as stress-relief heat treatments and water quenching, were crucial for reducing residual stresses and enhancing material integrity. They also visited the materials testing lab, where mechanical properties were rigorously evaluated to ensure aerospace-grade reliability.
High-pressure die casting at Exco Engineering
The next visit was to Exco Engineering, renowned for its expertise in the design and manufacturing of complex tooling systems for the die-cast and extrusion industries. The students were guided by Wessel Byleveld and Khaled Abu Samk, who showcased advanced CAD/CAM systems, precision machining, large scale metal additive manufacturing machinery and quality control processes. This visit allowed students to connect theoretical concepts from their coursework to the practical challenges of tooling design and manufacturing. Khaled was particularly approachable, engaging with students and thoroughly addressing their questions about the technical intricacies involved, while emphasizing the importance of precision and innovation in modern engineering.
At Exco Engineering, students delved into high-pressure die casting and large-scale CNC machining. Students also learned about additive manufacturing for metal lattice structures, followed by vacuum sintering to reduce porosity and improve density. This process also used uniform heating and reverse gravity casting to achieve precise thermal conductivity properties—critical for applications requiring rapid, uniform heat distribution in complex geometries.
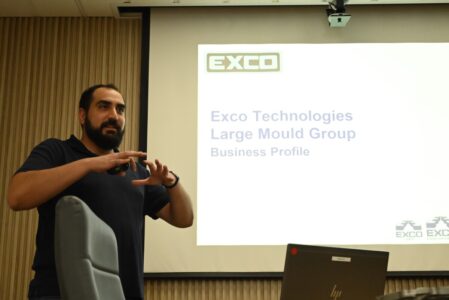
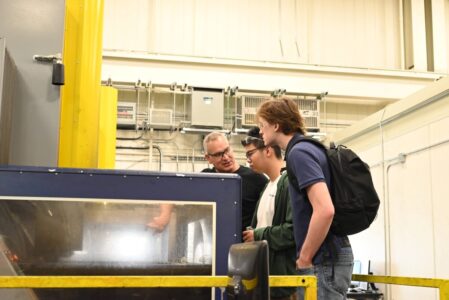
Automotive Innovation at Magna International
The final destination was Magna International, a global leader in automotive manufacturing. Here, students were welcomed by Aldo Van Gelder, Hongping Gu, and Danielle Starrett. Danielle shared insights about the company’s culture, emphasizing Magna’s commitment to innovation, collaboration, and employee development. Aldo and Hongping provided an in-depth look at the company’s state-of-the-art manufacturing processes, including a demonstration of how robotics and automation are integrated into vehicle production and how advanced manufacturing techniques are applied to create lightweight, high-strength components. This offered students a holistic view of the complexities involved in automotive manufacturing, highlighting the importance of a supportive work environment in maintaining high standards of quality and efficiency.
Additionally, Magna showcased advanced materials and processes used in automotive manufacturing, such as aluminum extrusion for lightweighting and the development of magnesium alloy components, including the GT3 RS roof for Porsche, which lowers the vehicle’s center of mass. Their R&D initiatives in robotic 3D/LIDAR scanning and laser-based surface hardening demonstrated the integration of automation in precision manufacturing and quality control.
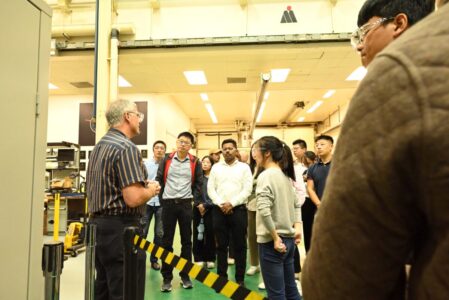
Connecting Classroom Learning to Industry Practice
The MSE industry tour underscored the vital connection between academic learning (e.g., MSE1068/MSE468 Additive Manufacturing of Advanced Engineering Materials) and industry practice, equipping students with the knowledge and skills necessary for future success. It provided a unique opportunity for students to witness firsthand how concepts from their coursework are applied in real-world scenarios. They gained a deeper appreciation for how Canadian manufacturing industries are incorporating cutting-edge technologies like additive manufacturing and the practical challenges of integrating advanced technologies into their processes. Students returned with a clearer perspective on potential career paths in this evolving field.
This event was financially supported by the Ontario Vehicle Innovation Network’s Regional Future Workforce (RFW) Program and led by Professor Zou’s research group and MSE students Ajay Talbot, Madhi Ramesh, Evelyn Li, and Tiani Lyu. The images and content for this newsletter was captured and prepared by Madhi Varshini Ramesh, with part of the content sourced from Theaswanth Ganesh’s LinkedIn post.